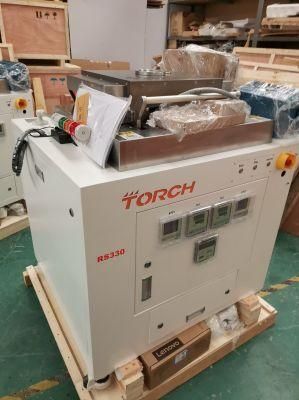
Formic Acid Vacuum Furnace
Termway (Beijing) Precision Technology Co., Ltd.- Condition:New
- Certification:ISO, CE
Base Info
- Model NO.:RS330
- Warranty:12 Months
- Automatic Grade:Semiautomatic
- Installation:Vertical
- Process Environment:Nitrogen, Formic Acid
- Soldering Area:330*330mm
- Chamber Height:>=100mm
- Max Temperature:500 C
- Maximum Vacuum:1X10-6bar
- Heating Elements:Infrared Heating Lamps
- Max. Heat up Ramp:120c,Minute
- Max. Cool Down Ramp:60-120,Minute
- Cooling Way:Nitrogen,Water-Cooled (Shell, Heating Plate)
- Heating Plate:Sic Coated Graphite
- Control Deviation:+,- 1°c
- Voltage:220V 25-60A
- Weight:360kg
- Transport Package:Polywood Case and Foam
- Specification:900*9000*1400mm
- Trademark:TORCH
- Origin:Beijing, China
- HS Code:8514101000
- Production Capacity:100 Set,Year
- Package size per unit product:900.00cm * 900.00cm * 1300.00cm
- Gross weight per unit product:375.000kg
Description
Basic Info.
Model NO. RS330 Warranty 12 Months Automatic Grade Semiautomatic Installation Vertical Process Environment Nitrogen, Formic Acid Soldering Area 330*330mm Chamber Height >=100mm Max Temperature 500 C Maximum Vacuum 1X10-6bar Heating Elements Infrared Heating Lamps Max. Heat up Ramp 120c/Minute Max. Cool Down Ramp 60-120/Minute Cooling Way Nitrogen/Water-Cooled (Shell, Heating Plate) Heating Plate Sic Coated Graphite Control Deviation +/- 1°c Voltage 220V 25-60A Weight 360kg Transport Package Polywood Case and Foam Specification 900*9000*1400mm Trademark TORCH Origin Beijing, China HS Code 8514101000 Production Capacity 100 Set/YearPackaging & Delivery
Package size per unit product 900.00cm * 900.00cm * 1300.00cm Gross weight per unit product 375.000kgProduct Description
Vacuum and Inert gas Atmosphere Vacuum sintering Reflow Oven RS330
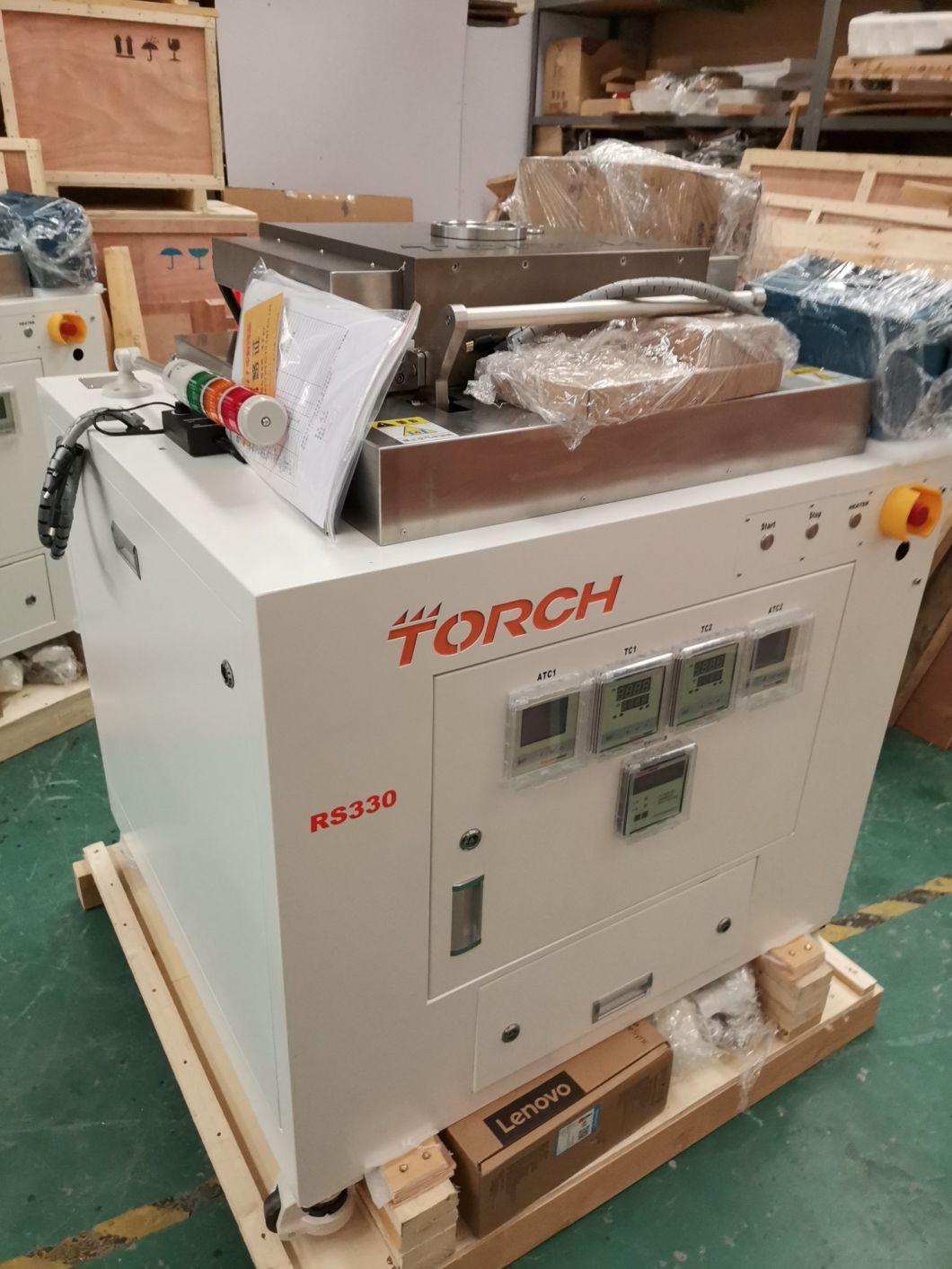
1. Soldering in a real vacuum atmosphere. Vacuum can be up to 10-3mpa, 10-6mpa optional
2. Low activity flux Soldering atmosphere.
3. Professional software control, to achieve good operation experience.
4. The programmable temperature control system of up to 40 sections can set perfect process curve.
5. The temperature setting can be adjusted to set up a process closer to the Soldering material process curve.
6. Water cooling technology to achieve rapid cooling effect (standard).
7. Online temperature measurement function. The temperature uniformity of Soldering area can be measured effectively. Provide support for process adjustment.
8. The nitrogen hydrogen mixture (a certain proportion of the mixture) or other inert gas is selected to meet the Soldering requirements of special process.
9. The maximum temperature is 600 ºC (higher optional), which meets all requirements of the soldering process.
10. The five systems are designed for safety status monitoring and safety protection (over temperature protection of Soldering parts, whole machine temperature safety protection, safe operation protection, cooling water circuit protection and power off protection during Soldering).
11. Simultaneous heating in both upper and lower parts.
Advantages:
1. Soldering temperature: the actual maximum Soldering temperature of RS220 vacuum Reflow Oven is ≥ 600 ºC.
2. Void ratio: peak value ≤ 10 Pa, working vacuum: 50pa-200pa.
3. Effective Soldering area: ≥ 220mm * 220mm
4. Furnace hearth height: ≥ 100 mm, other height can be custermized.
- Heating method: infrared radiation heating at the bottom and infrared radiation heating at the top.
6. Temperature uniformity: ≤± 2% within the effective Soldering area.
7. Heating rate: the maximum heating rate of graphite heating platform is ≤ 120 ºC / min.
RS220 vacuum Reflow Oven select to be heated in upper part, which can improve heating efficiency, temperature in platform will be more uniform, improve Soldering consistency and quality, and heating rate can be controlled.
8. Cooling rate: the maximum cooling rate is 80-120 ºC / min (no-load maximum temperature to 200 ºC).
Graphite heating platform: the combination of air cooling and water cooling is adopted to realize the rapid cooling of the hot plate and improve the cooling rate. In addition, poor sintering of the device caused by the excessive temperature difference in the cooling process can be avoided, and the cooling rate can be controlled through the process, while the requirements of slow cooling can be met as well.
9. Meet the Soldering requirements of Soldering items ≤ 600 ºC.
For example: in97ag3, in52sn48, Au80Sn20, sac305, sn90sb10, sn63pb37, sn62pb36ag2 and other preformed solder pads (can be eutectically Soldering without flux), various components of solder paste, and curing of materials below 600 ºC.
10. Soldering void ratio:
The void ratio of RS220 vacuum sintering furnace can be controlled within 0-3% during soft fiber solder Soldering, this is verified and concluded after a large number of customers' real use.
- Positive pressure module is optional:
This furnace can choose to be equipped with positive pressure module ≤ 0.3MPa, which can meet the requirements of positive pressure and negative pressure process. The positive pressure process can effectively solve the displacement problem of micro devices in the Soldering process (miniled, microled, etc.) and solve the flux spatter problem during solder paste process (lead frame products).
- Temperature control and measurement system
12.1 RS220 vacuum sintering furnace adopts the temperature control technology patented by TORCH, temperature control accuracy is ± 1 ºC.
12.2 RS220 vacuum sintering furnace temperature curve can be set up to more than 40 sections of temperature, and is equipped with 3 groups of PID settings, realizes more accurate control of temperature, ensure Soldering consistency and reliability. Temperature control is lagging control, and PID control has the function of advance adjustment, which can improve the accuracy and stability of temperature control.
12.3 RS220 vacuum sintering furnace cavity is equipped with four groups of temperature thermocouples as standard. When the furnace works, it can feed back the temperature of any position in the cavity in real time, and display the temperature curve in real time in the control software, so as to better ensure the temperature control of the Soldering area and provide support for obtaining good process curve.
13. Chamber atmosphere environment
The RS330 vacuum sintering furnace can be filled with nitrogen inert gas to assist Soldering and meet the requirements of formic acid reduction atmosphere process. The process atmosphere can be accurately controlled by time or MFC mass flowmeter to ensure the consistency of each set process. The equipment is equipped with a closed exhaust channel and a filtration system to process and discharge the waste gas through the exhaust channel to ensure the normal use of the equipment. It can be welded without flux.
Application:
IGBT/DBC
Power Semiconductors
Sensors
MEMS Devices
DIE Attachment
High Power LED
Hybrid Assembly
Flip Chip
Package Sealing
Company information:
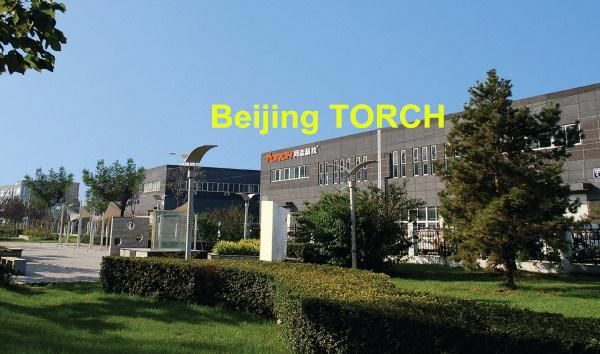
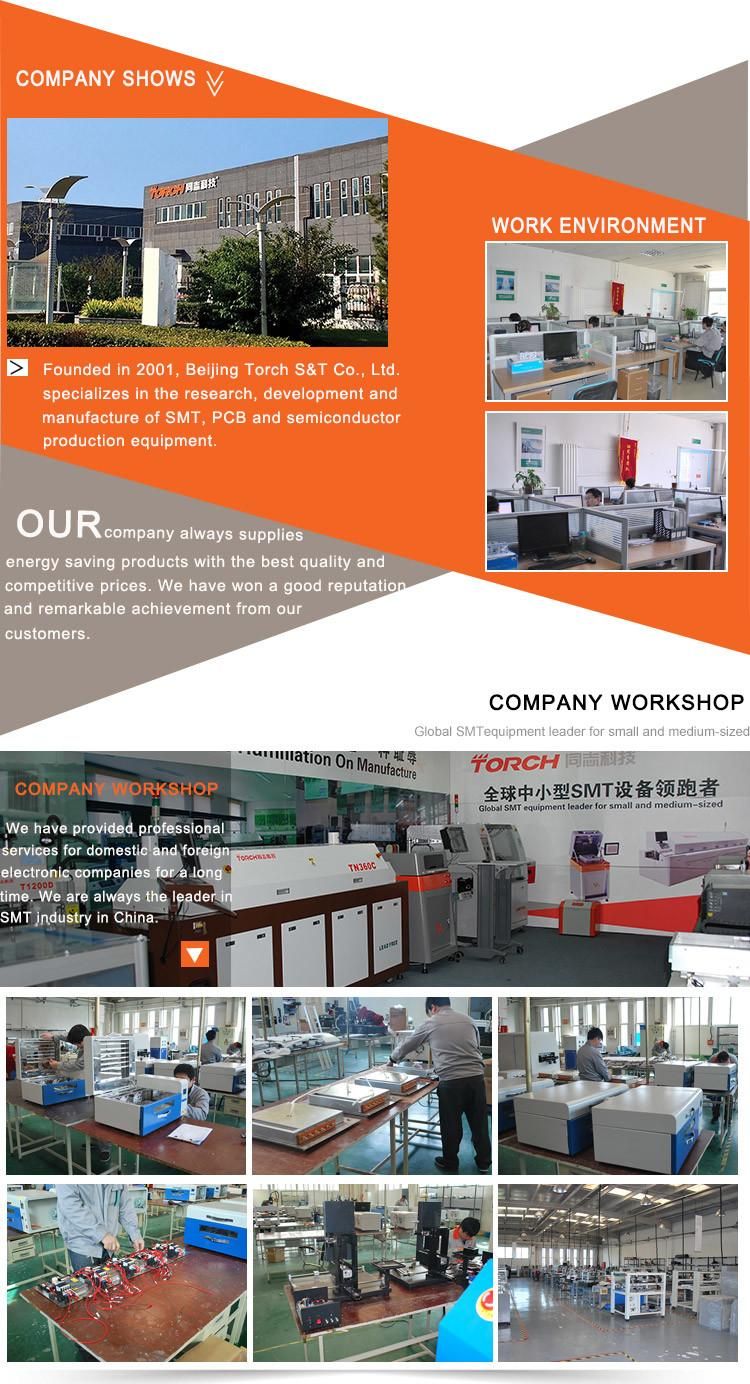
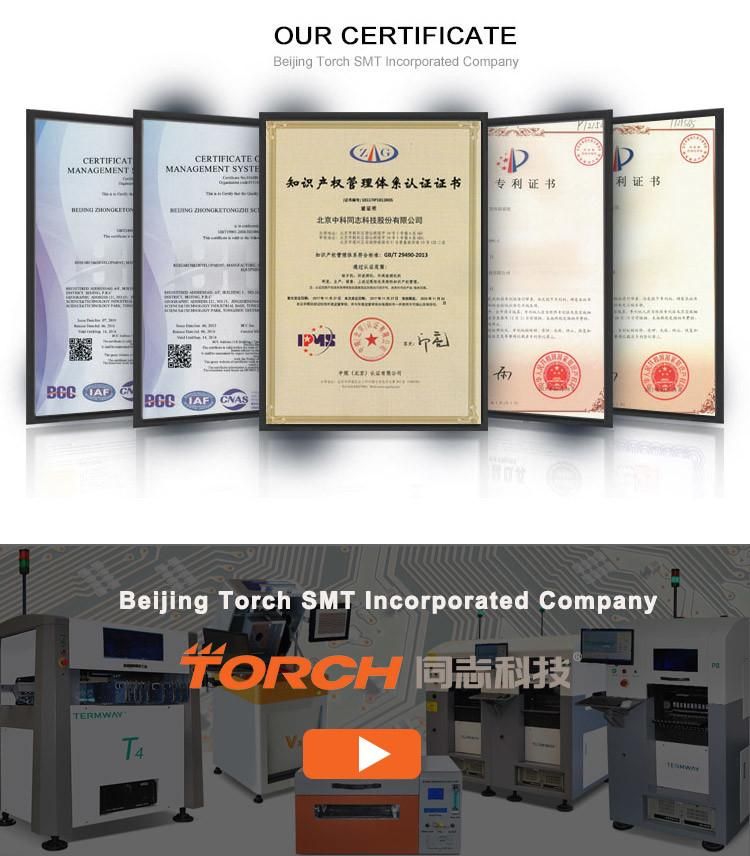